Leveraging Telemetry Data for Predictive Maintenance with Fyrefuse
While companies may believe that data center downtime is unavoidable, the truth is that data center failure can be predicted by adopting the proper technology.
Industry 4.0 supports the flexibility required for collaborative networks by the application of advanced technologies. Modern networks are characterized by interconnectedness where each node in addition to receiving, produces a vast amount of data enabling the collaborative chain to manage the production life cycle and demands effectively.
However, in such an interconnected environment, any single node’s failure is critical and might undermine the whole production process.
Benefits of Predictive Maintenance
Data centers use complex hardware that presents unforeseen problems that calendar-based maintenance checks simply cannot anticipate. Companies traditionally address the problem in two ways: either reactively (fixing the already existing failures) or proactively (using experience to anticipate potential breakdowns). Knowing well ahead of time when an asset will fail avoids unplanned downtimes and broken assets. Predictive maintenance strategy helps companies anticipate data center issues before they happen. On average, predictive maintenance increases productivity by 25%, reduces breakdowns by 70%, and lowers maintenance costs by 25%.
The benefits of predictive maintenance can be summarized in three points:
- First, costs saving for the company. On one side, the strategy’s predictive nature decreases planned maintenance fees; on the other side, the ability to reduce data center failures spares companies from suffering the massive costs associated with downtime.
- Second, predictive maintenance helps companies run their operations more effectively. The warning message of a machine can alert a worker, making it easier for maintenance to occur well before an issue escalates to the critical point.
- Finally, customers’ reputation is not damaged. Companies handle several kinds of data and must ensure service availability to customers. For this reason, even incremental downtimes can cause customers to lose trust in a company and take their business elsewhere.
AIOps Use Case with Fyrefuse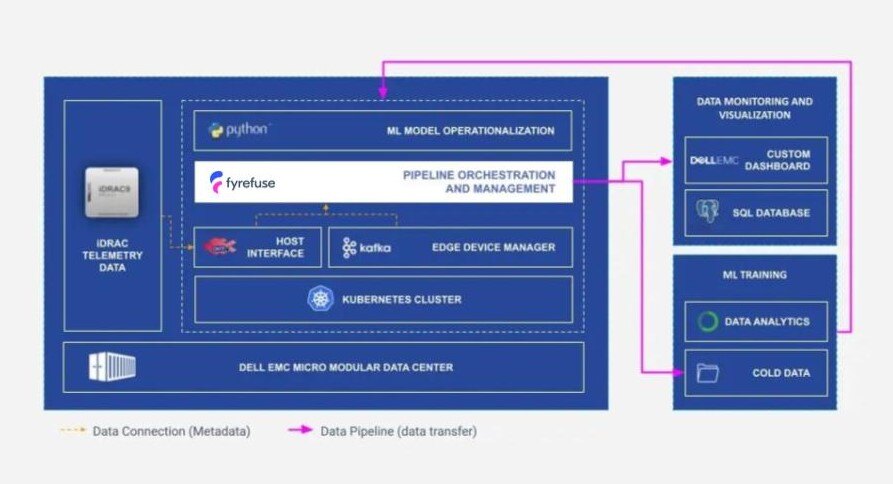
Our team has implemented a use case leveraging AIOps, which is short for artificial intelligence for IT operations, and telemetry data streaming for predictive maintenance of the Micro Modular Data Center in the Energy & Utility industry.
Telemetry is an automated communications process by which machine measurement data collected at remote or inaccessible points are transmitted for monitoring. Granular, time-series telemetry data is streamed, or pushed, compared to traditional pulling methods. Our team used advanced architecture with iDRAC9 that provides over 180 server-related data metrics, such as CPU metrics, storage logs etc. This comprehensive telemetry data is then fed into an AI engine to predict failure events, optimize server operation, and enhance cyber resiliency.
AIOps refers to a multi-layered technology platform that automates and enhances ITOps through analytics and ML by collecting a variety of data from various IT management tools and devices to automatically spot and react to issues in real-time, while still providing traditional historical analytics and enable the Customer to implement a cost-effective Predictive Maintenance strategy.
The final output of the use case is a technology system that leverages a streaming data analytics software architecture to:
- Ingest telemetry data generated within the hardware components of the partner into a streaming data pipeline.
- Analyze collected data in real-time by Machine Learning algorithms.
- Publish predictions and recommendations over the analyzed data (future faults of the connected hardware components) on a web-based dashboard.
Conclusion
All companies that wish to remain competitive and avoid huge losses in the future must adopt predictive maintenance practices.
Fyrefuse can help manage data flows and productionalise AI to reduce efforts and pain on maintenance planning time and increase equipment uptime and availability.